
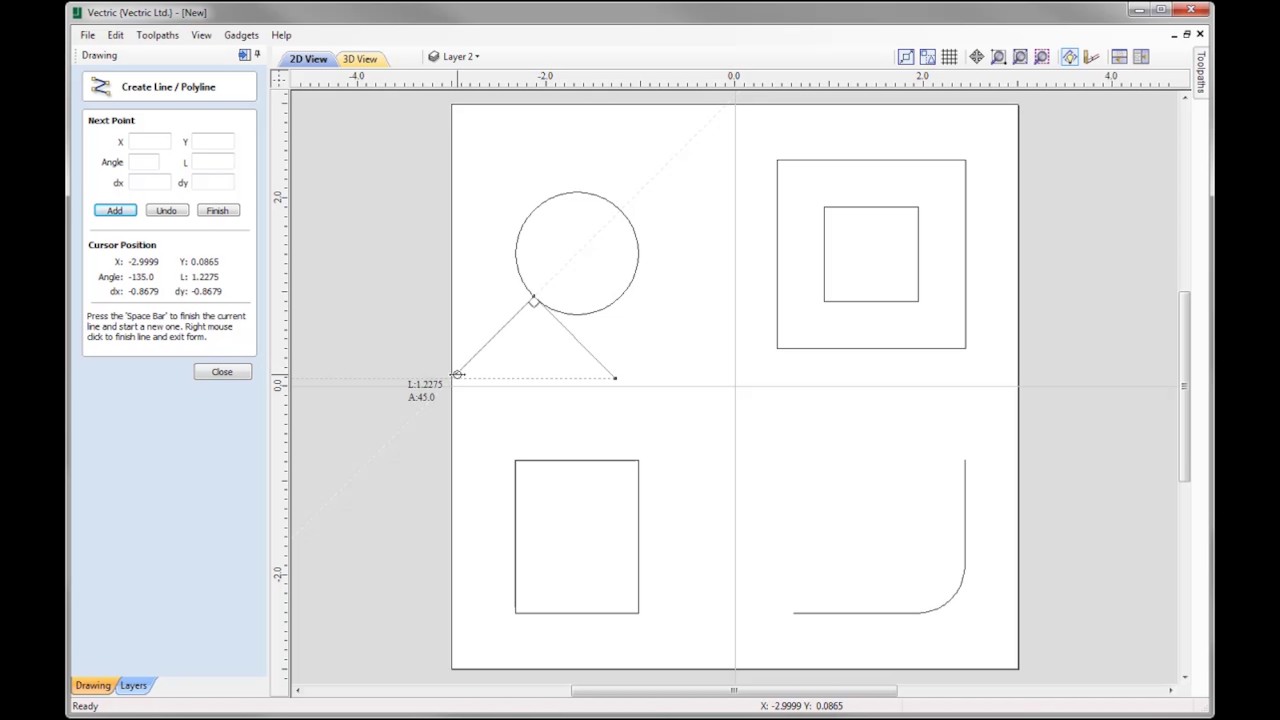
- #VECTRIC VCARVE PRO FORCE DRILL IN ONE DIRECTION SOFTWARE#
- #VECTRIC VCARVE PRO FORCE DRILL IN ONE DIRECTION PC#
one last question, ive seen parallel PCI computer cards. I also have an extra computer thats not in use. i recently saw some steppers at a local surplus shop that appeared bigger than most of what was used for the smaller mills for around $15 each. So, i have the table, the drill, and access to surplus stores. the limited lateral force on a drill press should handle that. also, it would be NICE if possible to be able to cut rectangular sockets (for AC inlets, computer ports, etc.) out of thin aluminum (maybe 1/16" or 1/8" thick). not terribly so, but i just want stuff to be lined up right. What i "need" to do is make a machine that drills precisely. it has some play in it, but i can fix that. i just recently bought a milling table off ebay. i understand that they dont make great milling machines becuase they dont like a whole lot of lateral force. I currently have a 12" drill press thats 2/3HP i think (its a craftsman). So, here is what i'm after for now: well, answers of course, but here is what i am trying to build/accomplish: im pretty good with this stuff, but the information thats out there is really hard to grasp. as soon as im done, im posting all the stuff in a NICE Q&A on my website (which is a pretty good amount of visitors in the DIY audio realm.). do you always start from a zero point, or do you just have to "zero" the workpiece?
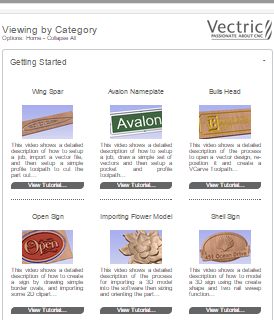
however, what feedback is there to tell the machine where the bit is at a given time, and where it NEEDS to be? is there a way to zero the machine without feedback from the computer? it seems like you can move the bit, map the bit's movements, but the computer seemingly has no idea where the bit actually is.
#VECTRIC VCARVE PRO FORCE DRILL IN ONE DIRECTION SOFTWARE#
Lastly, ive seen a whole lot of software that appears like it can do CAM functions. it is all in the form of steps (which i understand), but do you have to just know how many steps is equal to an inch, or is there some interpretation? next, how does the software communicate exactly? i dont care about the technical details, but if i want to make two holes, 3 inches apart, how do i say, "move three inches right". why is this? what is the main difference?
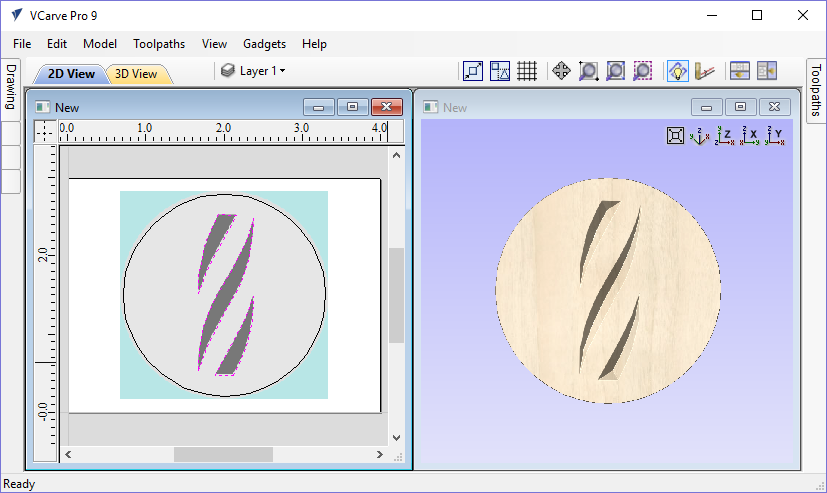
i see many in the $50-$100 price range, and then some in the multiple $100's range. I see MANY controllers online and most look almost identical, but prices vary a lot. 179 says it can control a motor through a PC, or direct, and you can hook up to 6 motors to a single PC. I found a few stepper motor controllers on (kits 179, and 113 i think).

this also leads into my confusion about software. what i DONT understand is how you link stepper software, controllers, motors, etc.
#VECTRIC VCARVE PRO FORCE DRILL IN ONE DIRECTION PC#
and i understand you can control a stepper with PC software. Next, i get that steppers need controllers. BUT, for my purposes, this is irrelevant. but, im still trying to grasp what makes a milling machine a milling machine, and not just a beefy drill press. i understand the differences in chucks and lateral forces. i am somewhat unsure of how a "milling machine" is different than lets say a drill press. i know generally what size to get (the biggest i can get surplus ) i know the more steps, the better, etc. i know i will be using stepper motors (for cost and for simplicity). Next, i am familiar with stepper motors, servo motors, and movement. i know that its an computer-based interpretation/control system that reads input (from a file or from a user) and manipulates a machine. i generally know what a CNC machine is (the original goal was to make a CNC-type machine), that led me to the research. ive collected a lot, and know a lot more than i did, but little of it fits all together. every day i find something new and confusing. ive gotten into several hobbies through the years, and i must say, this one has a TON of scattered information. i came across this site while doing some research on my own.
